Pada 2 Mei 1953, penerbangan perdana de Havilland Comet, pesawat jet komersial pertama di dunia, menandai fajar baru dalam perjalanan udara. Namun, dalam waktu kurang dari setahun, dua pesawat Comet hancur di udara tanpa peringatan. Investigasi mengungkap penyebab yang mengerikan: kegagalan lelah (fatigue failure) yang berasal dari sudut jendela persegi, sebuah fitur desain yang tampaknya sepele. Tragedi ini menjadi pelajaran pahit bagi dunia rekayasa, menyoroti musuh tak terlihat yang dihadapi setiap insinyur: material dapat gagal pada tegangan yang jauh di bawah batas kekuatannya jika dikenai beban berulang.
Masalah mendasar ini tetap menjadi tantangan utama hingga hari ini, terutama dalam industri dirgantara di mana keselamatan adalah hal mutlak. Insinyur terus berjuang melawan pertanyaan: bagaimana cara mencegah kegagalan katastropik yang dimulai dari cacat mikroskopis?
Panduan definitif ini hadir untuk menjawab pertanyaan tersebut. Kami akan menjembatani kesenjangan antara teori abstrak dan aplikasi praktis, dengan menyajikan kerangka kerja yang kohesif yang menghubungkan penyebab (kondisi dan kekasaran permukaan), mekanisme (konsentrasi tegangan), dan solusi (desain cerdas, pemilihan material, dan perlakuan permukaan canggih). Dalam artikel ini, Anda akan belajar memahami, menganalisis, dan pada akhirnya mengalahkan kegagalan lelah dengan menguasai ilmu tentang permukaan.
- Memahami Kegagalan Lelah: Musuh Tak Terlihat dalam Rekayasa Material
- Peran Krusial Permukaan: Bagaimana Kekasaran Memulai Kegagalan Lelah
- Analisis Kegagalan Lelah: Membaca Kisah dari Permukaan Patahan
- Toolkit Insinyur: Strategi Komprehensif untuk Meningkatkan Umur Lelah
- Studi Kasus: Menjamin Integritas Permukaan pada Komponen Pesawat Kritis
- Kesimpulan: Mengalahkan Kegagalan Dimulai dari Permukaan
- Referensi dan Sumber
Memahami Kegagalan Lelah: Musuh Tak Terlihat dalam Rekayasa Material
Dalam dunia rekayasa, kekuatan material sering kali diukur dengan kemampuannya menahan satu beban besar (beban statis). Namun, sebagian besar komponen mesin dan struktur, terutama pada pesawat terbang, tidak mengalami satu beban tunggal, melainkan jutaan siklus pembebanan dan pelepasan (beban siklik) selama masa pakainya—mulai dari getaran mesin hingga siklus tekanan kabin. Di sinilah konsep ketahanan lelah material menjadi sangat penting.
Ketahanan lelah adalah kemampuan suatu material untuk menahan beban siklik atau berulang tanpa mengalami kegagalan. Kegagalan yang terjadi akibat beban berulang ini disebut kegagalan lelah. Ini adalah fenomena berbahaya karena terjadi secara tiba-tiba dan tanpa deformasi yang jelas, sering kali pada tingkat tegangan yang dianggap aman di bawah beban statis. Faktanya, diperkirakan bahwa lebih dari 90% dari semua kegagalan layanan mekanis disebabkan oleh kelelahan.[1]
Perbedaan antara kegagalan statis dan kegagalan lelah sangat mendasar. Bayangkan membengkokkan klip kertas. Jika Anda menariknya dengan kuat sekali, ia akan bengkok atau patah—ini adalah kegagalan statis. Namun, jika Anda membengkokkannya bolak-balik berulang kali dengan gaya yang lebih kecil, ia akhirnya akan patah—ini adalah kegagalan lelah.
Konsekuensi dari kegagalan lelah bisa sangat menghancurkan. Insiden Aloha Airlines Flight 243 pada tahun 1988, di mana sebagian besar atap badan pesawat robek di tengah penerbangan, adalah contoh nyata dari kegagalan lelah yang meluas akibat ribuan siklus tekanan selama lepas landas dan mendarat.
Proses kegagalan lelah ini umumnya terjadi dalam tiga tahap yang berbeda:
- Inisiasi Retak (Crack Initiation): Tahap pertama dimulai pada tingkat mikroskopis. Retakan kecil mulai terbentuk di area dengan tegangan tinggi, hampir selalu di permukaan komponen.
- Perambatan Retak (Crack Propagation): Dengan setiap siklus beban, retakan kecil ini tumbuh sedikit lebih besar, merambat lebih dalam ke dalam material.
- Patahan Akhir (Final Fracture): Retakan terus merambat hingga sisa penampang material yang utuh tidak lagi cukup kuat untuk menahan beban. Pada titik ini, kegagalan akhir terjadi secara tiba-tiba dan katastropik.
Memahami ketiga tahap ini adalah kunci untuk mencegahnya, dan seperti yang akan kita lihat, pertempuran melawan kegagalan lelah hampir selalu dimulai dari permukaan.
Peran Krusial Permukaan: Bagaimana Kekasaran Memulai Kegagalan Lelah
Jika kegagalan lelah adalah sebuah cerita, maka bab pertamanya hampir selalu ditulis di permukaan material. Permukaan yang tampak halus dengan mata telanjang sebenarnya adalah lanskap pegunungan dan lembah pada tingkat mikroskopis. “Lembah-lembah” mikroskopis ini, baik yang berasal dari proses manufaktur, goresan saat servis, atau korosi, adalah titik awal dari malapetaka.
Fenomena ini dijelaskan oleh konsep konsentrasi tegangan. Ketika sebuah komponen dibebani, tegangan (gaya per satuan luas) didistribusikan ke seluruh bagiannya. Pada komponen dengan permukaan yang sangat halus dan geometri yang seragam, distribusi ini relatif merata. Namun, setiap takik, goresan, atau “lembah” pada permukaan mengganggu aliran tegangan ini, memaksanya untuk “mengumpul” di dasar cacat tersebut. Akibatnya, tegangan lokal di ujung goresan bisa berkali-kali lipat lebih tinggi daripada tegangan nominal pada komponen secara keseluruhan.
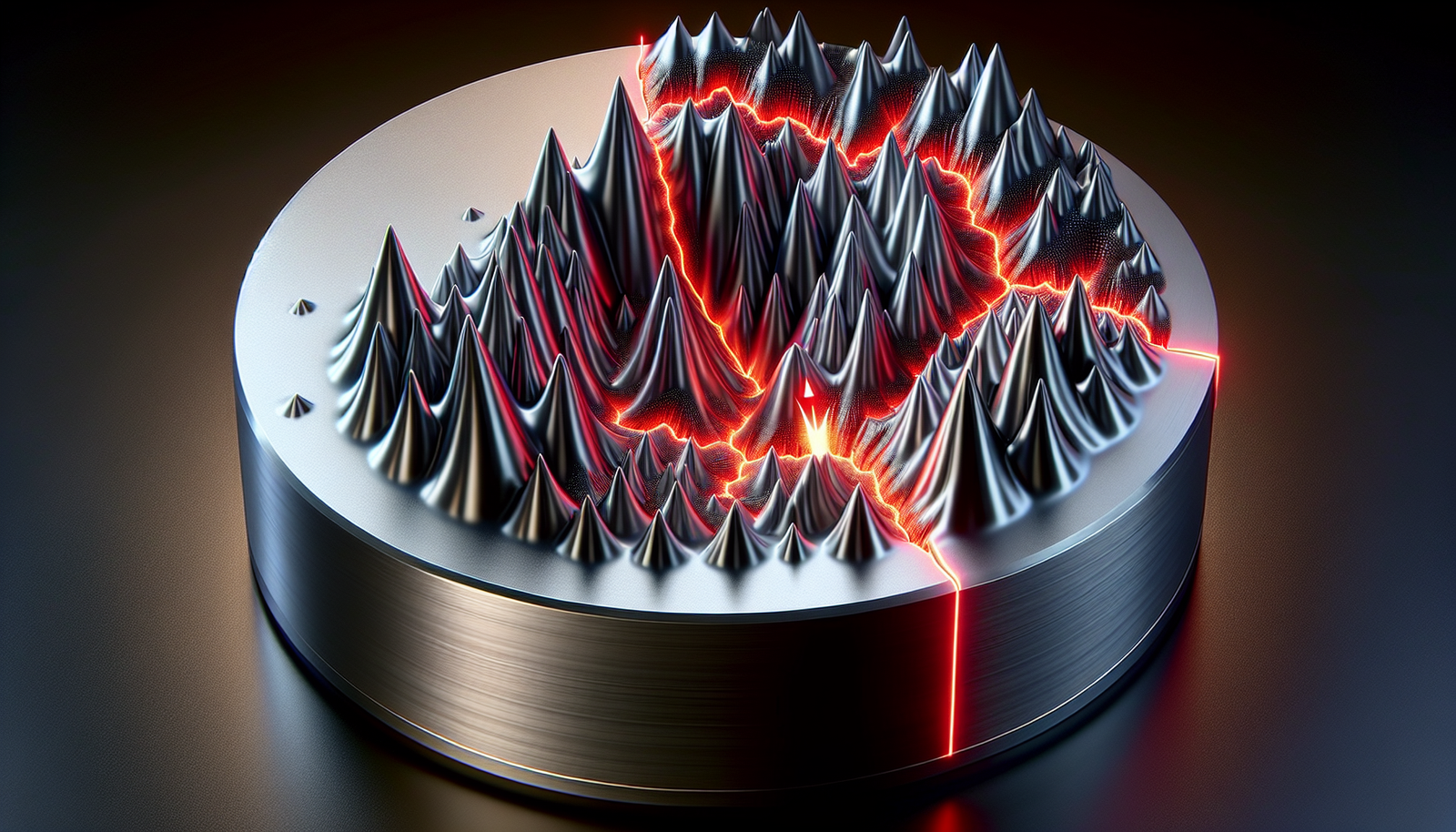
Untuk mengukur dan mengontrol kekasaran permukaan, insinyur menggunakan beberapa parameter, yang paling umum adalah:
- Ra (Roughness Average): Nilai rata-rata aritmatika dari semua puncak dan lembah dari garis tengah profil permukaan. Ini memberikan gambaran umum tentang kehalusan.
- Rz (Maximum Height of Profile): Jarak vertikal antara puncak tertinggi dan lembah terdalam dalam sampel pengukuran. Parameter ini penting karena lembah yang dalam dapat menjadi konsentrator tegangan yang parah.
Area dengan tegangan yang sangat terkonsentrasi ini menjadi lokasi utama untuk inisiasi retak lelah. Sebagaimana dinyatakan dalam sebuah studi yang diterbitkan di jurnal Micromachines, “Goresan mikro di permukaan…dianggap ‘cacat lelah’. Cacat ini dapat menyebabkan konsentrasi tegangan yang melemahkan ketahanan material terhadap kegagalan…”.[3]
Dampak dari kekasaran permukaan ini tidak hanya teoritis, tetapi juga terukur secara kuantitatif. Data dari produsen komponen teknis menunjukkan bahwa pada baut baja paduan tinggi 40CrNiMo, penurunan kualitas permukaan (peningkatan kekasaran) dapat mengurangi kekuatan lelah sebesar 21% hingga 33%.[2] Ini adalah penurunan drastis dalam kinerja yang disebabkan oleh fitur permukaan yang tidak terlihat.
Konsentrasi Tegangan vs. Tegangan Permukaan: Mengklarifikasi Kebingungan Umum
Dalam diskusi tentang permukaan, penting untuk mengklarifikasi dua istilah yang sering membingungkan: konsentrasi tegangan dan tegangan permukaan. Meskipun keduanya melibatkan kata “tegangan” dan “permukaan,” keduanya adalah konsep fisika yang sama sekali berbeda dan tidak dapat dipertukarkan.
Fitur | Konsentrasi Tegangan (Stress Concentration) | Tegangan Permukaan (Surface Tension) |
---|---|---|
Domain Fisika | Mekanika Benda Padat (Solid Mechanics) | Mekanika Fluida (Fluid Mechanics) |
Definisi | Lokalisasi tegangan tinggi di sekitar diskontinuitas geometris (takik, lubang, goresan) pada benda padat yang dibebani. | Kecenderungan molekul cairan untuk saling tarik-menarik di permukaan, menciptakan lapisan elastis tipis (misalnya, serangga berjalan di atas air). |
Penyebab | Geometri komponen (lubang, fillet, kekasaran permukaan). | Gaya kohesif antar molekul cairan. |
Relevansi | Faktor utama penyebab inisiasi retak lelah pada komponen mekanis. | Menentukan bagaimana cairan membasahi permukaan, membentuk tetesan, dan fenomena kapilaritas. |
Konsekuensi | Mengurangi kekuatan lelah dan umur komponen secara signifikan. | Tidak relevan secara langsung dengan kegagalan mekanis benda padat. |
Singkatnya, untuk insinyur yang berurusan dengan durabilitas komponen pesawat, konsentrasi tegangan adalah fenomena kritis yang harus dikelola, sementara tegangan permukaan adalah konsep yang relevan dalam domain yang berbeda seperti hidrodinamika atau ilmu pelapisan.
Analisis Kegagalan Lelah: Membaca Kisah dari Permukaan Patahan
Ketika sebuah komponen gagal, permukaan patahannya menyimpan bukti berharga yang menceritakan kisah kegagalannya. Bagi seorang insinyur material, menganalisis permukaan patahan ini—sebuah proses yang disebut fraktografi—adalah seperti melakukan pekerjaan detektif forensik. Permukaan patahan akibat kelelahan memiliki ciri khas yang membedakannya dari jenis patahan lainnya.
Dengan menggunakan alat seperti Mikroskop Elektron Pemindai (Scanning Electron Microscope/SEM), para ahli dapat mengidentifikasi fitur-fitur kunci. Permukaan patahan lelah yang khas akan menunjukkan tiga zona yang berbeda:
- Situs Inisiasi (Initiation Site): Titik asal retakan. Ini sering kali merupakan area yang relatif kecil dan halus, yang hampir selalu dapat dilacak kembali ke cacat permukaan seperti goresan mesin, lubang korosi, atau inklusi material di dekat permukaan.
- Tanda Pantai (Beachmarks/Striations): Saat retakan merambat melalui material dengan setiap siklus beban, ia meninggalkan serangkaian tanda samar yang melengkung dan konsentris yang memancar keluar dari situs inisiasi. Tanda-tanda ini, yang disebut beachmarks (tanda pantai), terlihat seperti riak di pasir dan menandai posisi ujung retakan pada berbagai waktu. Setiap beachmark mewakili periode perambatan retakan.
- Zona Patahan Cepat Akhir (Final Fast Fracture Zone): Ini adalah area terakhir yang patah. Setelah retakan merambat cukup jauh, sisa material tidak lagi mampu menahan beban, dan patah secara tiba-tiba. Zona ini biasanya memiliki penampilan yang kasar dan berserat, khas dari patahan akibat kelebihan beban.
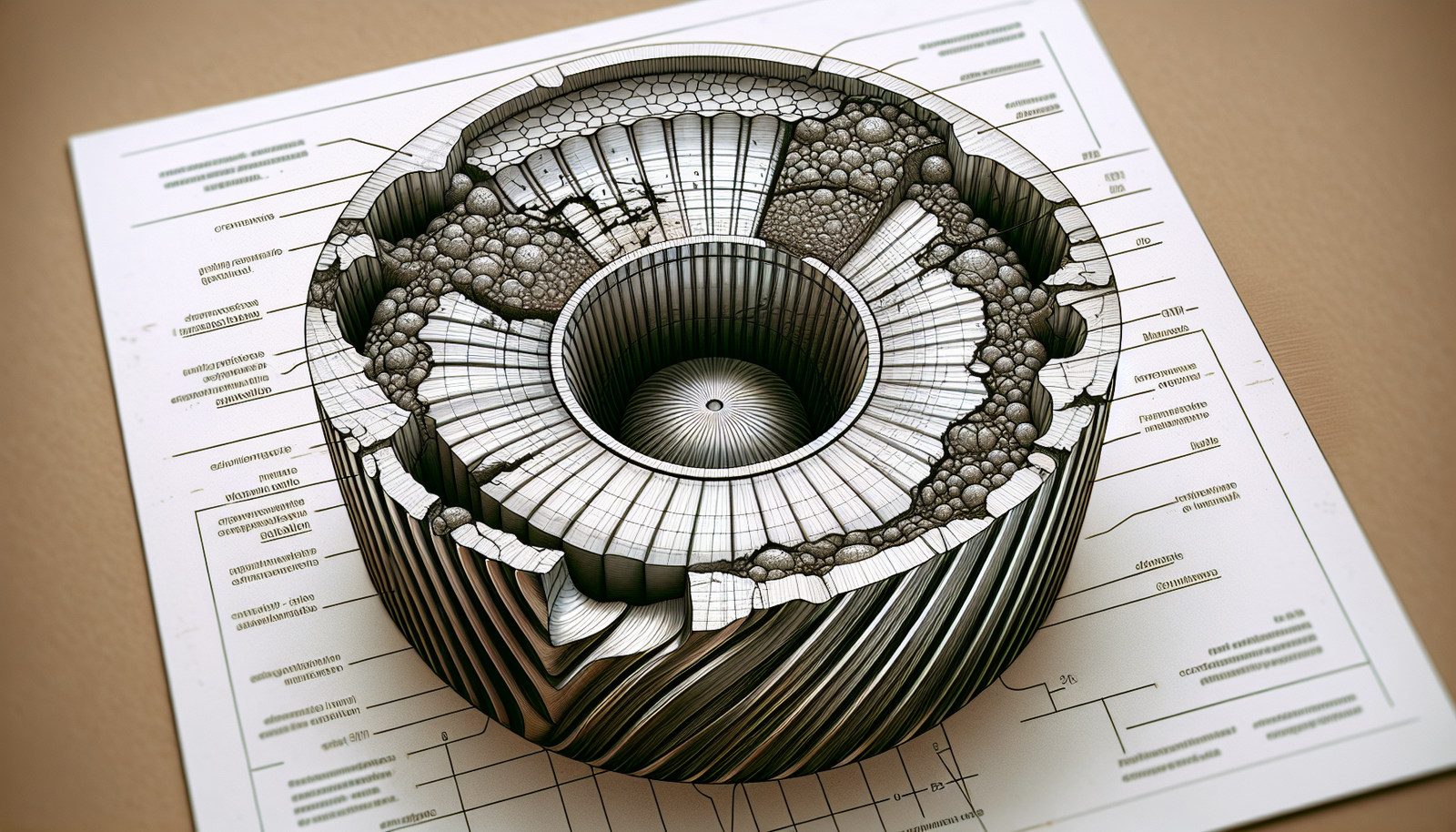
Metodologi analisis kegagalan yang kredibel, seperti yang didukung oleh penelitian dari lembaga seperti Badan Riset dan Inovasi Nasional (BRIN) Indonesia,[4] sangat penting untuk menentukan akar penyebab dan mencegah kejadian serupa di masa depan.
Berikut adalah daftar periksa sederhana untuk analisis kegagalan lelah dasar:
- Langkah 1: Inspeksi Visual: Periksa komponen yang gagal secara keseluruhan. Cari lokasi patahan utama.
- Langkah 2: Identifikasi Situs Inisiasi: Periksa permukaan patahan dengan hati-hati (jika perlu dengan pembesaran rendah). Cari titik awal retakan di tepi atau permukaan.
- Langkah 3: Cari Tanda Pantai: Cari pola beachmarks yang khas yang memancar dari situs inisiasi. Kehadiran mereka adalah bukti kuat dari kegagalan lelah.
- Langkah 4: Periksa Zona Patahan Akhir: Identifikasi area yang kasar dan berserat yang menunjukkan kegagalan akhir yang cepat. Ukuran relatif zona ini dapat memberikan petunjuk tentang tingkat tegangan saat kegagalan.
- Langkah 5: Analisis Mikroskopis (jika diperlukan): Gunakan SEM untuk memeriksa situs inisiasi secara detail dan mengkonfirmasi keberadaan striasi mikroskopis di dalam beachmarks.
Dengan membaca kisah yang tertulis di permukaan patahan, insinyur dapat memperoleh wawasan tak ternilai tentang bagaimana dan mengapa komponen gagal, yang mengarah langsung ke pengembangan solusi yang lebih baik.
Toolkit Insinyur: Strategi Komprehensif untuk Meningkatkan Umur Lelah
Mencegah kegagalan lelah bukanlah tentang satu solusi ajaib, melainkan tentang menerapkan strategi pertahanan berlapis yang mencakup seluruh siklus hidup komponen. Seperti yang dinyatakan dalam referensi industri definitif, ASM Handbook, “Ketahanan… terhadap kelelahan juga dipengaruhi oleh prosedur manufaktur seperti pembentukan dingin, pengelasan, mematri, dan pelapisan dan oleh kondisi permukaan seperti kekasaran permukaan dan tegangan sisa.”[5] Kerangka kerja komprehensif ini dapat dibagi menjadi tiga pilar utama: desain cerdas, pemilihan material strategis, dan perlakuan permukaan canggih.
1. Desain Cerdas: Mencegah Retak Sebelum Terbentuk
Pertahanan terbaik melawan kegagalan lelah sering kali dimulai di papan gambar digital. Prinsip utama desain tahan lelah adalah untuk meminimalkan atau menghilangkan konsentrasi tegangan sejak awal. Ini berarti menghindari perubahan geometri yang tiba-tiba dan tajam.
- Hindari Sudut Tajam: Sudut internal yang tajam adalah konsentrator tegangan yang parah. Sebaliknya, desainer harus selalu menggunakan fillet (sudut internal yang dibulatkan) dengan radius sebesar mungkin.
- Gunakan Transisi yang Mulus: Perubahan penampang, seperti dari poros tebal ke poros tipis, harus dilakukan secara bertahap dengan transisi yang landai atau tirus, bukan dengan “bahu” yang tajam.
- Posisikan Lubang dengan Hati-hati: Lubang dan potongan lainnya harus ditempatkan jauh dari area bertegangan tinggi jika memungkinkan.
Prinsip-prinsip ini, yang merupakan inti dari buku pegangan desain mesin seperti Shigley’s Mechanical Engineering Design, adalah garis pertahanan pertama dan paling hemat biaya untuk memastikan umur lelah yang panjang.
2. Pemilihan Material Strategis untuk Material Pesawat
Tidak semua material diciptakan sama dalam hal ketahanan lelah. Untuk aplikasi kritis seperti pesawat terbang, pemilihan material yang tepat adalah keputusan fundamental yang mempengaruhi keselamatan dan efisiensi.
Material | Kelebihan | Kekurangan | Contoh Aplikasi Pesawat |
---|---|---|---|
Paduan Aluminium (Seri 7000, mis. 7075-T6) | Rasio kekuatan-terhadap-berat yang sangat baik, dapat diprediksi sifat lelahnya, biaya relatif rendah. | Rentan terhadap korosi, ketahanan lelah lebih rendah dari titanium. | Struktur sayap atas, rangka badan pesawat. |
Paduan Titanium (mis. Ti-6Al-4V) | Ketahanan lelah dan korosi yang luar biasa, kinerja suhu tinggi yang baik. | Biaya tinggi, sulit untuk dimesin. | Komponen mesin kritis, roda pendarat, spar sayap. |
Material Komposit (Serat Karbon/Epoksi) | Rasio kekuatan-terhadap-berat tertinggi, ketahanan lelah yang sangat baik, dapat disesuaikan sifatnya. | Mode kegagalan kompleks (delaminasi), sensitif terhadap benturan, biaya manufaktur tinggi. | Badan pesawat (Boeing 787, Airbus A350), permukaan kontrol, ekor. |
Penggunaan material komposit telah merevolusi desain pesawat modern. Menurut BRIN, “Penggunaan material komposit di pesawat biasanya berkisar antara 20% hingga 50%”,[6] sebagian besar karena sifat ketahanan lelahnya yang unggul dibandingkan logam tradisional. Pemilihan material harus selalu dipandu oleh persyaratan spesifik aplikasi dan standar yang ditetapkan oleh otoritas penerbangan seperti FAA (Federal Aviation Administration) dan EASA (European Union Aviation Safety Agency).
3. Perlakuan Permukaan: Pertahanan Terakhir dan Paling Kuat
Setelah komponen dirancang dan material dipilih, lapisan pertahanan terakhir—dan sering kali yang paling kuat—adalah rekayasa permukaan itu sendiri. Perlakuan permukaan dapat secara dramatis meningkatkan ketahanan lelah dengan menghaluskan cacat atau, yang lebih penting, dengan mengubah sifat permukaan. Seperti yang ditekankan oleh penelitian modern, “topografi, tegangan sisa, dan deformasi adalah aspek yang paling penting untuk dipertimbangkan” saat memastikan kinerja lelah yang tinggi.[7]
Beberapa teknik kunci meliputi:
- Polishing/Finishing: Proses seperti penggilingan halus, lapping, dan pemolesan secara fisik menghilangkan lapisan permukaan yang kasar, menghilangkan potensi situs inisiasi retak.
- Shot Peening: Ini adalah proses kerja dingin di mana permukaan komponen “ditembaki” dengan media bulat kecil (shot). Setiap tumbukan bertindak sebagai palu kecil, menciptakan lekukan dan meregangkan permukaan. Peregangan ini menghasilkan lapisan tegangan sisa tekan (compressive residual stress) yang sangat bermanfaat di permukaan. Tegangan tekan ini harus diatasi oleh tegangan tarik dari beban eksternal sebelum retakan dapat terbentuk, sehingga secara dramatis meningkatkan umur lelah.
- Perlakuan Termokimia (Nitriding/Carburizing): Proses ini melibatkan difusi atom (seperti nitrogen atau karbon) ke permukaan baja pada suhu tinggi. Ini menciptakan lapisan permukaan yang sangat keras dan tahan aus yang juga memiliki tegangan sisa tekan yang tinggi, meningkatkan ketahanan aus dan lelah. Nitriding, misalnya, umum digunakan untuk poros engkol otomotif dan roda gigi.
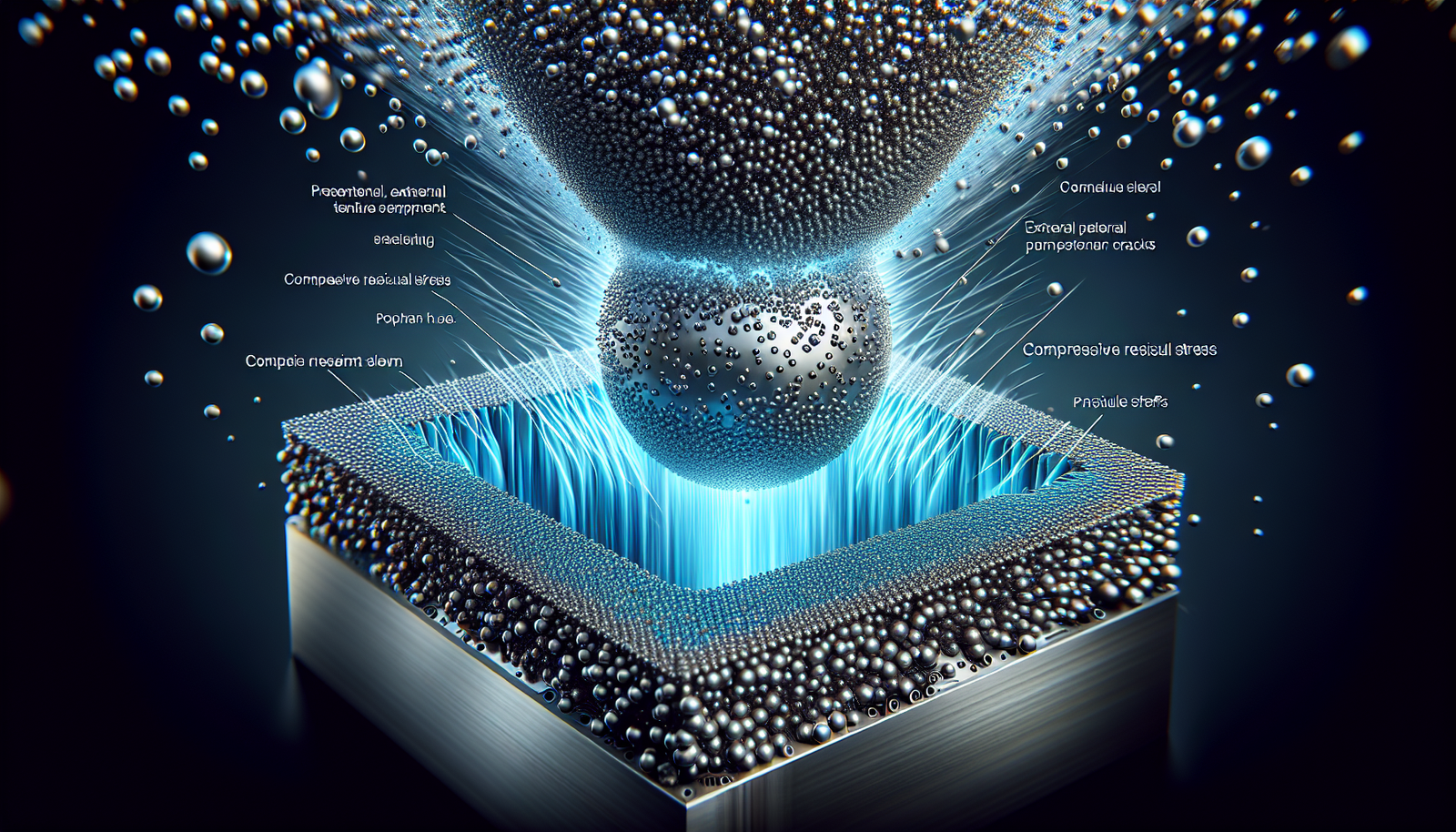
Memilih perawatan yang tepat bergantung pada material, aplikasi, dan masalah yang ingin dipecahkan.
Masalah | Solusi Perlakuan Permukaan | Material Umum |
---|---|---|
Inisiasi Retak Lelah | Shot Peening, Polishing | Baja, Aluminium, Titanium |
Keausan & Lelah | Nitriding, Carburizing | Baja Paduan |
Korosi & Lelah | Anodizing, Pelapisan PVD | Aluminium, Baja |
Studi Kasus: Menjamin Integritas Permukaan pada Komponen Pesawat Kritis
Mari kita satukan semua konsep ini dalam konteks pesawat terbang modern. Keamanan penerbangan bergantung pada jaminan integritas setiap komponen, dari kulit badan pesawat hingga bilah turbin mesin.
Bayangkan sebuah spar sayap, tulang punggung struktural sayap. Komponen ini mengalami siklus lentur yang luar biasa selama setiap penerbangan.
- Desain & Material: Spar ini dirancang dengan fillet yang besar dan transisi yang mulus. Ia mungkin dibuat dari paduan aluminium kekuatan tinggi seperti 7075-T6 atau, untuk pesawat performa tinggi, paduan titanium.
- Manufaktur & Finishing: Setelah dimesin, permukaan kritisnya tidak dibiarkan dalam kondisi ‘apa adanya’. Permukaan tersebut akan menjalani proses finishing presisi untuk mencapai kehalusan permukaan yang sangat rendah, menghilangkan semua bekas alat mesin.
- Perlakuan Permukaan: Selanjutnya, area kritis spar tersebut kemungkinan besar akan menjalani proses shot peening untuk menginduksi tegangan sisa tekan yang protektif, menciptakan “pelindung” tak terlihat terhadap inisiasi retak lelah.
- Pengujian & Verifikasi: Sebelum dipasang, sampel material dan komponen prototipe akan diuji secara ketat sesuai dengan standar industri seperti ASTM E466 – Standard Practice for Conducting Force Controlled Constant Amplitude Axial Fatigue Tests of Metallic Materials.[8] Penelitian modern, seperti yang dilakukan pada paduan kedirgantaraan Inconel 718, bahkan menggunakan model canggih untuk memprediksi umur lelah secara akurat berdasarkan pengukuran integritas permukaan pasca-pemesinan.[7]
- Inspeksi Seumur Hidup: Selama masa pakai pesawat, komponen seperti spar sayap akan diperiksa secara berkala menggunakan teknik Pengujian Non-Destruktif (Non-Destructive Testing/NDT) seperti inspeksi arus eddy atau penetran pewarna untuk mendeteksi retakan permukaan sekecil apa pun sebelum dapat merambat ke tingkat yang berbahaya.
Pendekatan berlapis ini—dari desain hingga material, manufaktur, perawatan, dan inspeksi—adalah cara industri dirgantara mengelola musuh tak terlihat dari kegagalan lelah dan menjaga langit tetap aman.
Kesimpulan: Mengalahkan Kegagalan Dimulai dari Permukaan
Tragedi de Havilland Comet mengajarkan dunia rekayasa sebuah kebenaran abadi: kegagalan katastropik sering kali berawal dari detail terkecil. Perjalanan kita melalui ilmu ketahanan lelah telah menegaskan kembali pelajaran ini, menunjukkan bahwa pertempuran melawan kegagalan material hampir selalu dimenangkan atau dikalahkan di permukaannya.
Kita telah melihat bahwa:
- Kelelahan dimulai di permukaan: Cacat mikroskopis, goresan, dan kekasaran adalah tempat lahirnya retakan yang fatal.
- Konsentrasi tegangan adalah mekanismenya: Ketidaksempurnaan permukaan memperkuat tegangan lokal, menyediakan energi yang dibutuhkan untuk memulai kegagalan.
- Solusinya adalah pendekatan holistik: Kombinasi desain cerdas untuk meminimalkan tegangan, pemilihan material yang tahan lelah, dan perlakuan permukaan canggih untuk menciptakan permukaan yang kuat adalah satu-satunya cara untuk memastikan durabilitas jangka panjang.
Dengan memahami hubungan kritis antara kondisi permukaan dan ketahanan lelah, insinyur diberdayakan untuk beralih dari sekadar bereaksi terhadap kegagalan menjadi secara proaktif merancang komponen yang dapat menahan kerasnya layanan di dunia nyata. Ini adalah inti dari rekayasa yang bertanggung jawab dan kunci untuk membangun masa depan yang lebih aman dan lebih andal.
Bagikan panduan ini dengan rekan insinyur Anda atau tinggalkan komentar di bawah dengan pertanyaan atau pengalaman Anda sendiri dalam menangani kegagalan lelah.
Disclaimer: Artikel ini ditujukan untuk tujuan informasi dan pendidikan teknik. Informasi yang disajikan tidak boleh dianggap sebagai pengganti analisis, desain, atau konsultasi rekayasa profesional untuk aplikasi kritis apa pun.
Referensi dan Sumber
- Jurnal Rekayasa Material, Manufaktur dan Energi. (N.D.). Analisis Laju Perambatan Retak Lelah pada Material Baja Tahan Karat Austenitik 304 dengan Variasi Amplitudo Beban. UMSU.
- Jinrui Bolt. (N.D.). Beberapa Faktor Yang Harus Diketahui Mempengaruhi Baut Kekuatan Tinggi. id.jinruibolts.com.
- Zhang, P., Wang, Z., Kang, R., Dong, Z., & Guo, D. (2022). Study of Surface Integrity of Titanium Alloy (TC4) by Belt Grinding to Achieve the Same Surface Roughness Range. Micromachines, 13(11), 2003. https://pmc.ncbi.nlm.nih.gov/articles/PMC9697110/
- Surojo, E., & Ariatedja, J. B. (2019). Analisis Kegagalan Komponen Mesin. Majalah Ilmiah Pengkajian Industri. ejournal.brin.go.id.
- ASM International. (N.D.). Effect of Surface Condition and Processing on Fatigue Performance. ASM Handbook, Volume 19: Fatigue and Fracture. https://dl.asminternational.org/handbooks/edited-volume/chapter-pdf/505633/a0002371.pdf
- Badan Riset dan Inovasi Nasional (BRIN). (2024). BRIN Kembangkan Komposit untuk Pesawat Ramah Lingkungan dan Ekonomis. brin.go.id.
- Holmberg, J., Wretland, A., Berglund, J., & Beno, T. (2021). Surface integrity investigations for prediction of fatigue properties after machining of alloy 718. International Journal of Fatigue, 144. https://www.sciencedirect.com/science/article/pii/S0142112320305910
- ASTM International. (N.D.). ASTM E466 – Standard Practice for Conducting Force Controlled Constant Amplitude Axial Fatigue Tests of Metallic Materials.